What is quality control methods?
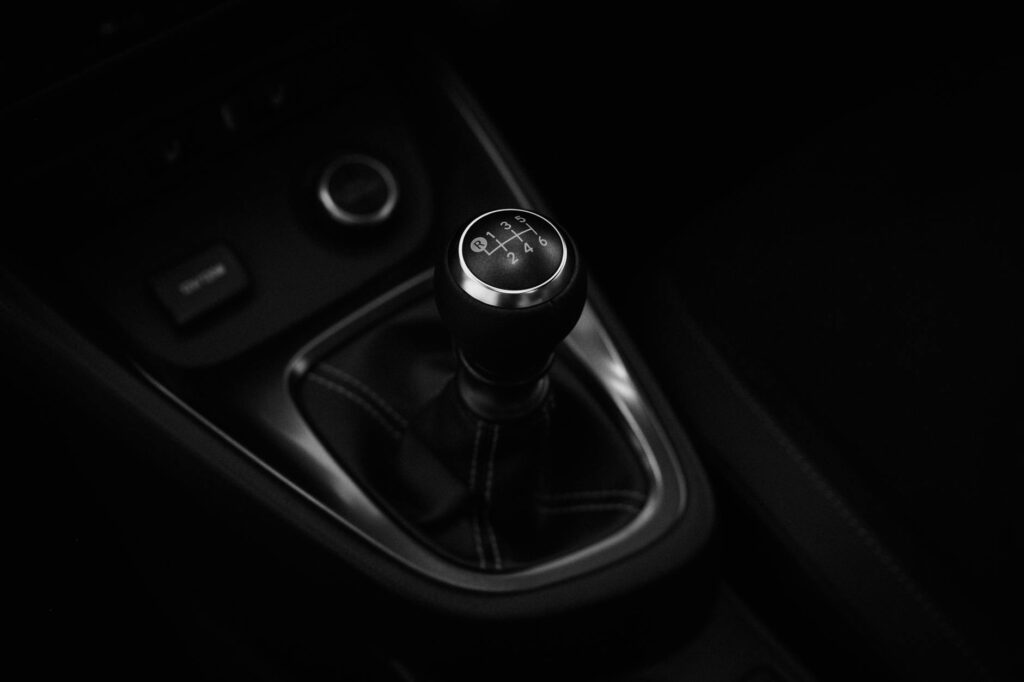
What is quality control methods?
Quality control methods are essential practices that ensure products and services meet specific standards of excellence. In every industry, from manufacturing to food services, maintaining high quality is crucial for customer satisfaction and business success. As customers become more discerning, businesses must prioritize quality control to enhance their offerings and retain a loyal customer base. By understanding and implementing effective quality control methods, companies can not only meet but exceed customer expectations.
Understanding Quality Control
Quality control refers to the systematic process of ensuring that products or services are designed and produced to meet or exceed specified quality standards. It encompasses various techniques and practices aimed at detecting defects, reducing variability, and ensuring consistent quality in the production process.
Definition of Quality Control
At its core, quality control is a set of activities designed to evaluate the quality of a product or service. This involves assessing the characteristics of the output against predetermined standards and specifications. The goal is to identify any deviations from these standards and rectify them promptly to maintain quality.
Importance of Quality Control Methods
Why are quality control methods critical for businesses? For starters, they help maximize profits by reducing waste and minimizing the costs associated with rework and defects. Additionally, effective quality control fosters customer loyalty. When customers receive high-quality products consistently, they’re more likely to return and recommend the business to others. According to Indeed, quality control ensures that customers receive products free from errors or defects, leading to increased satisfaction.
Types of Quality Control Methods
Various quality control methods are utilized across different industries, each tailored to specific needs and requirements.
Statistical Process Control (SPC)
Statistical Process Control (SPC) is a method that employs statistical analysis to monitor and control a process. By using control charts, businesses can track data over time to identify trends and variations. This approach allows organizations to detect problems before they escalate, ensuring that processes remain within defined limits.
Total Quality Management (TQM)
Total Quality Management (TQM) is a comprehensive approach to improving quality at all levels of an organization. It emphasizes continuous improvement, employee involvement, and customer satisfaction. TQM involves everyone in the organization, from top management to front-line employees, working together to enhance quality across all processes.
Six Sigma
Six Sigma is a data-driven methodology that aims to improve quality by identifying and removing the causes of defects. This method focuses on process improvement and variance reduction, helping organizations achieve near perfection in their products and services. Companies that adopt Six Sigma often see significant reductions in costs and improvements in customer satisfaction.
Inspection and Testing
Inspection and testing are fundamental components of quality control. Various techniques, such as visual inspections, destructive testing, and non-destructive testing, are employed to assess quality. These methods ensure that products meet quality standards before they reach the customer.
Implementing Quality Control Methods
Establishing effective quality control methods requires a structured approach. Here are key steps for implementation:
Defining Quality Standards
The first step in quality control is defining clear quality standards that align with business objectives. These standards provide a benchmark against which products can be measured. Establishing these criteria involves understanding customer expectations and regulatory requirements.
Training and Involvement of Staff
Training employees on quality control practices is crucial for success. When staff members understand their role in maintaining quality, they are more likely to take ownership and actively participate in quality initiatives. Regular training sessions can help reinforce the importance of quality control and keep staff updated on best practices.
Monitoring and Continuous Improvement
Quality control is not a one-time effort. Continuous monitoring of processes and outcomes is necessary to ensure sustained quality. Regular assessments, audits, and feedback loops should be established to identify areas for improvement. This approach fosters a culture of continuous improvement, encouraging organizations to innovate and adapt.
Challenges in Quality Control
While implementing quality control methods is vital, several challenges can arise during the process.
Resistance to Change
One of the most significant challenges is resistance to change within an organization. Employees may be hesitant to adopt new processes or practices, especially if they feel comfortable with existing methods. Overcoming this resistance requires effective communication and a focus on the benefits of quality control.
Resource Constraints
Limited resources can also hinder effective quality control. Small businesses, in particular, may struggle to allocate sufficient time and budget for quality initiatives. However, even with limited resources, organizations can implement basic quality control practices to improve outcomes gradually.
Conclusion and Best Practices
Quality control methods are essential for any organization aiming to achieve excellence in its products or services. By understanding the various techniques available and implementing them effectively, businesses can not only meet customer expectations but also foster loyalty and improve profitability.
Final Thoughts on Quality Control Methods
Prioritizing quality control is not just about meeting standards; it’s about creating a culture that values excellence at every level. Embrace quality control methods in your practice, and continuously seek improvement. Remember, in a world where consumers have endless choices, quality can be your competitive edge.
Photo by Ayyeee Ayyeee