What is continuous improvement processes?
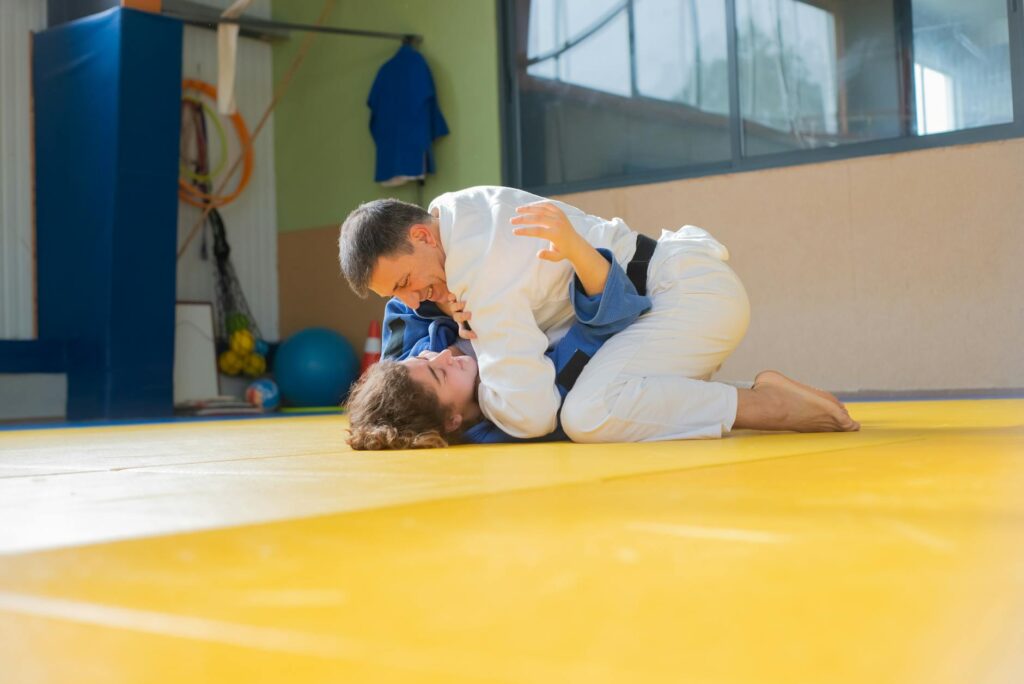
What is Continuous Improvement Processes?
Continuous improvement processes are all about making small, incremental changes to enhance efficiency, quality, and overall performance. These processes can be applied in various environments, including workplaces and personal development. They focus on improving workflows, products, and services by learning from experiences and feedback. Embracing continuous improvement can lead to significant progress over time, transforming the way we work and live.
Understanding Continuous Improvement Processes
At its core, continuous improvement processes are methods that organizations use to evaluate their performance and implement enhancements. The aim is to create a culture of ongoing improvement where everyone contributes to better practices. This can lead to increased satisfaction among employees and customers alike.
Core Principles of Continuous Improvement
The foundation of continuous improvement rests on several key principles:
-
Incremental Change: Instead of sweeping changes, continuous improvement advocates for small, manageable adjustments. Think of it like taking baby steps rather than trying to leap to the finish line.
-
Customer Focus: Understanding and responding to customer needs is vital. Continuous improvement emphasizes listening to feedback and making adjustments accordingly.
-
Employee Involvement: Everyone in the organization should feel empowered to suggest improvements. When employees are engaged, they often provide valuable insights that can lead to meaningful changes.
These principles encourage a proactive approach, where potential issues are addressed before they escalate, fostering a more efficient and harmonious work environment.
Benefits of Continuous Improvement Processes
Adopting continuous improvement processes offers a wide range of advantages, including:
-
Enhanced Productivity: By streamlining processes and reducing waste, organizations can boost productivity. This often leads to higher output with the same resources.
-
Improved Quality: Continuous feedback and adjustments help maintain high-quality standards. This becomes evident in product development and customer service.
-
Higher Employee Engagement: When employees participate in the improvement process, they feel valued. This engagement can lead to lower turnover rates and improved morale.
-
Cost Reduction: By eliminating inefficiencies and optimizing processes, organizations can significantly reduce costs. The savings can then be reinvested into further improvements.
For a more comprehensive look at the benefits, check out the insights on The Importance of Continuous Improvement.
Implementing Continuous Improvement Processes
Integrating continuous improvement into daily routines requires a structured approach. Here are some steps to consider:
Identifying Areas for Improvement
The first step in the process is recognizing where improvements can be made. Techniques such as process mapping, customer feedback surveys, and performance metrics can help uncover inefficiencies. Ask yourself: What tasks take longer than expected? Where do bottlenecks occur?
Tools and Techniques for Continuous Improvement
Several methodologies can aid in the implementation of continuous improvement processes:
-
PDCA (Plan-Do-Check-Act): This cyclical model encourages planning changes, implementing them, evaluating results, and making necessary adjustments.
-
Lean Methodology: Focused on maximizing value while minimizing waste, Lean principles can lead to more efficient processes.
-
Six Sigma: This data-driven approach aims to reduce defects and improve quality by identifying and removing causes of errors.
For an in-depth understanding of these tools, check out What is Continuous Improvement: Tools and Methodologies.
Challenges in Continuous Improvement Processes
While the benefits are clear, organizations may encounter hurdles when adopting continuous improvement processes.
Resistance to Change
Change can be daunting. Employees may resist new processes due to fear of the unknown or discomfort with altering their routines. To combat this, it’s essential to communicate the benefits clearly and involve employees in the decision-making process.
Maintaining Momentum
Sustaining improvement efforts over time can be challenging. Organizations need to cultivate a culture where continuous improvement is part of the DNA. Regularly revisiting improvement goals and celebrating successes can help keep motivation high.
Case Studies of Successful Continuous Improvement
Real-world examples illustrate the effectiveness of continuous improvement processes.
Company A: Transforming Operations
Company A implemented Lean practices to streamline its manufacturing processes. By continuously assessing workflows and involving employees in identifying inefficiencies, they reduced production time by 30%. This significant improvement boosted output and reduced costs.
Company B: Boosting Customer Satisfaction
Company B focused on enhancing customer experience through continuous improvement. By gathering customer feedback and regularly adjusting their service approach, they increased customer satisfaction scores significantly. This resulted in higher customer retention rates and increased referrals.
Conclusion: Embracing Continuous Improvement Processes
Integrating continuous improvement processes in both personal and professional contexts can lead to remarkable growth. By focusing on incremental changes, engaging employees, and maintaining a customer-centric approach, you can enhance efficiency and drive success. The journey of continuous improvement is ongoing, and every step taken is a leap towards achieving greater outcomes. Embrace this mindset and watch as improvements become a natural part of your work and life.
Photo by Kampus Production