What is continuous improvement models?
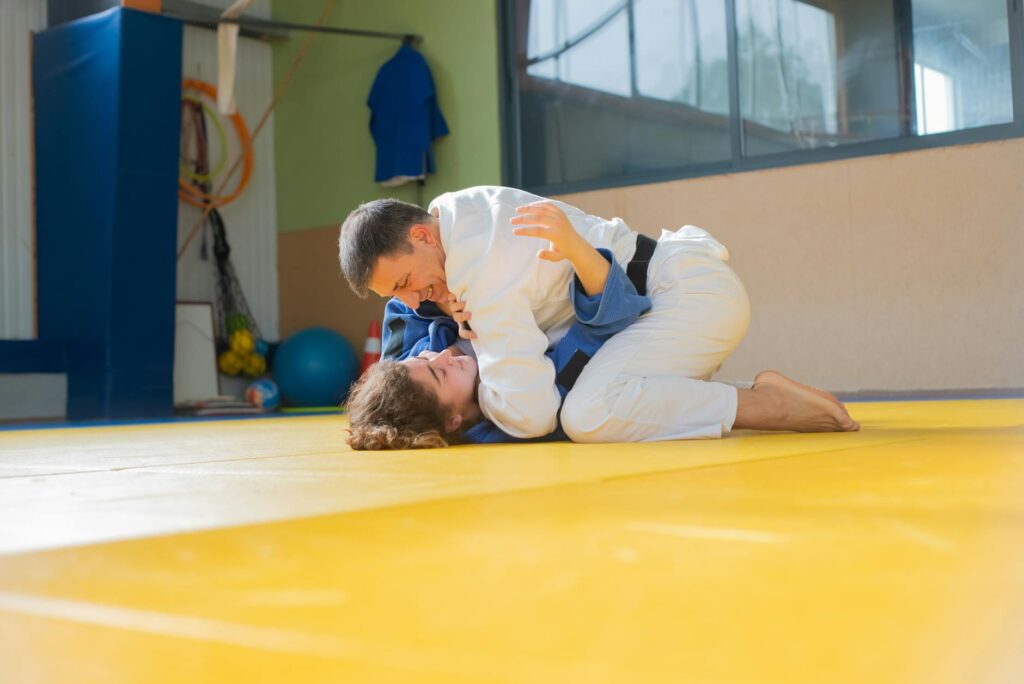
What is Continuous Improvement Models?
Continuous improvement models are structured approaches aimed at enhancing processes, products, and services over time. These models are vital in both personal and professional settings, promoting a culture of ongoing development. Understanding and applying these models can significantly boost productivity and effectiveness, whether in a corporate environment or in your personal life.
Imagine you’re trying to make a phone call, but your signal keeps dropping. You wouldn’t simply accept that as normal, would you? Instead, you’d likely explore ways to improve the signal, whether by switching carriers or changing your location. This analogy captures the essence of continuous improvement: always seeking better ways to achieve desired outcomes.
Understanding Continuous Improvement Models
Continuous improvement models focus on the principle that small, incremental changes can lead to significant improvements over time. They provide a framework for organizations and individuals to evaluate their current processes, identify inefficiencies, and implement changes that enhance overall performance.
Defining Continuous Improvement
At its core, continuous improvement is about making processes better. This involves regularly assessing practices and seeking ways to improve efficiency, reduce waste, and enhance quality. The principles of continuous improvement can be applied across various contexts, from manufacturing to personal productivity.
In manufacturing, for example, continuous improvement can lead to faster production times and reduced costs. In personal life, it could mean optimizing daily routines to save time and increase satisfaction. The key is the commitment to ongoing assessment and adaptation.
The Benefits of Continuous Improvement Models
Implementing continuous improvement models can yield several advantages:
- Increased Efficiency: Streamlining processes reduces wasted time and resources. You can find more about this on Leanscape.
- Enhanced Quality: Regular evaluations lead to higher quality products and services.
- Employee Engagement: Involving team members in improvement initiatives boosts morale and productivity.
- Better Customer Satisfaction: Improved processes lead to better outcomes for customers, enhancing loyalty and retention.
- Cost Reduction: By minimizing waste, organizations can cut costs while maintaining quality.
By adopting these models, you can create a sustainable environment of growth and development, personally and professionally.
Popular Continuous Improvement Models
Several continuous improvement models are widely recognized and utilized across industries. Each offers unique strategies and methodologies to foster improvement.
The Plan-Do-Check-Act (PDCA) Cycle
The PDCA cycle is a foundational approach in continuous improvement. It consists of four stages:
- Plan: Identify an opportunity and plan for change.
- Do: Implement the change on a small scale.
- Check: Review the results and analyze what happened.
- Act: If the change was successful, implement it on a larger scale.
This cyclical process encourages ongoing adjustments and refinements.
Photo by Kampus Production
Lean Principles
The Lean approach emphasizes eliminating waste and maximizing value. This model helps organizations focus on what truly matters to customers, ensuring that every step in a process adds value. By concentrating on efficiency, teams can streamline operations, reducing costs and improving output.
Six Sigma Methodology
Six Sigma is another powerful continuous improvement model. It focuses on quality enhancement and process control through data-driven decision-making. Six Sigma employs statistical methods to identify defects and variances in processes, aiming for a goal of no more than 3.4 defects per million opportunities. This model is particularly valuable in manufacturing and service industries.
Implementing Continuous Improvement Models
Incorporating continuous improvement models into your daily routines and work processes can seem daunting, but it’s manageable with practical steps.
Setting Clear Objectives
Establishing specific, measurable goals is crucial for success. Without clear objectives, it’s challenging to assess progress. Whether you’re aiming to reduce waste or improve customer satisfaction, clearly defined goals provide a roadmap for your improvement efforts.
Measuring Progress and Success
Tracking improvements over time helps gauge the effectiveness of implemented changes. Use tools and metrics relevant to your goals to monitor progress. Regular assessments will allow you to adjust your strategies as needed and celebrate your successes, no matter how small.
Challenges and Considerations
While continuous improvement models offer numerous benefits, adopting them isn’t always smooth sailing.
Resistance to Change
Many people and organizations resist change due to comfort with the status quo. This resistance can stem from fear of the unknown or previous negative experiences. Addressing these concerns through open communication and involving team members in the improvement process can facilitate smoother transitions.
Maintaining Momentum
Once improvements are made, it’s essential to sustain the momentum. Create a culture of continuous improvement where feedback is valued, and innovation is encouraged. Regular check-ins and celebrations of successes can help keep the team motivated to continue striving for excellence.
Conclusion
Continuous improvement models are essential for anyone looking to enhance their personal or professional life. By embracing these principles, you can foster a culture of growth and efficiency. Whether you’re implementing the PDCA cycle, Lean principles, or Six Sigma, the path to improvement is always available. So why wait? Start applying these concepts today and watch how they transform your approach to achievements and productivity.